Manufacturing Setup
State of the Art Manufacturing Facilities
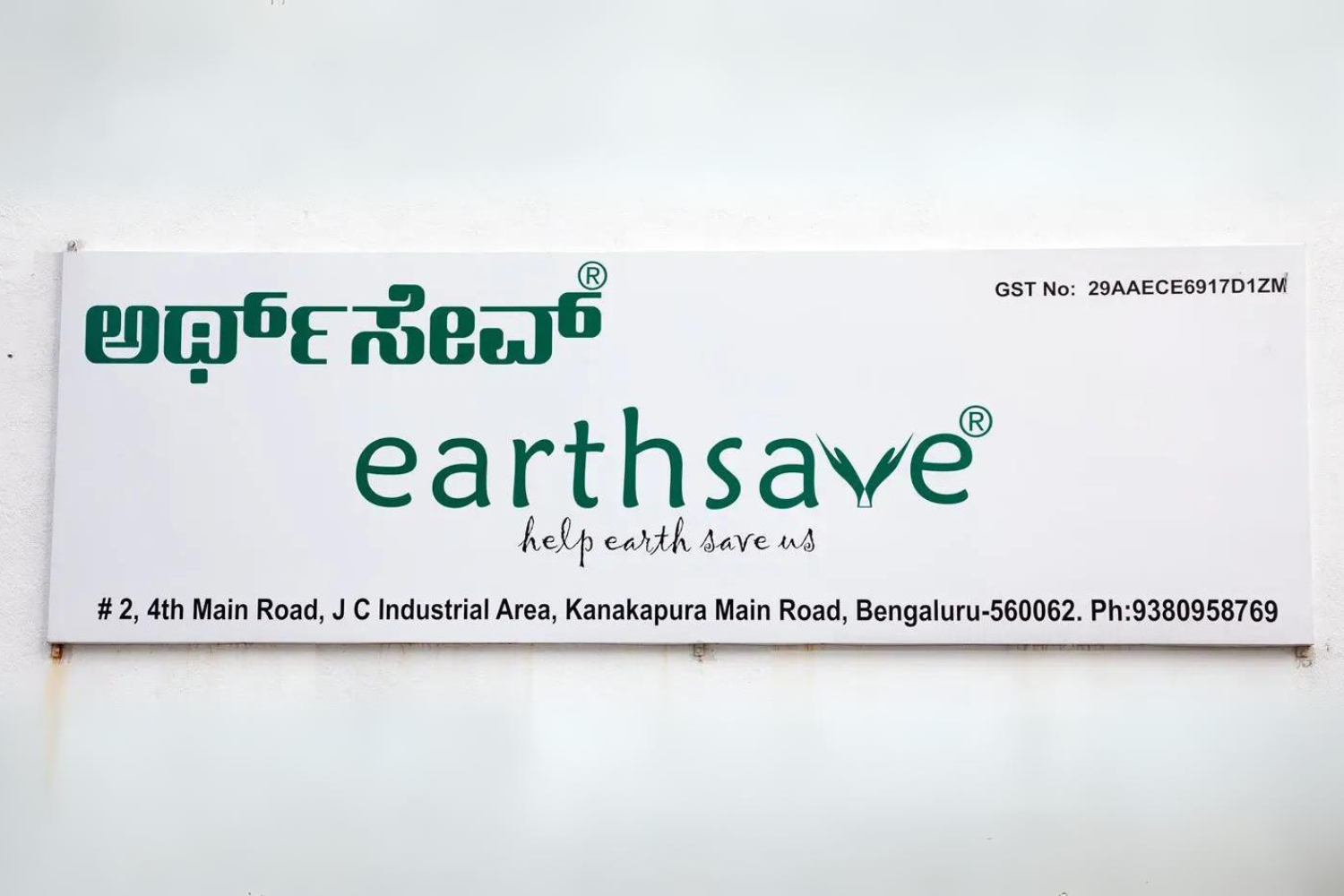
ABOUT THE COMPANY
We have established four comprehensive end to end manufacturing facilities in Karnataka, India to create world-class eco-friendly products. We design and produce awesome cotton bags and masks, leading the world to a more sustainable Earth, which we all know is the only one we have.
Earthsave Manufacturing Process

Fabric Store
We have a designated well-lit space for storage of our fabrics at each of our locations. All fabrics are quantity and quality before inwards. The area is well defined and demarcated for each particular variety of fabric, mills etc. A very efficient store in charge and his team ably supported by an effective software makes our fabric store one of the most organized and up to date.
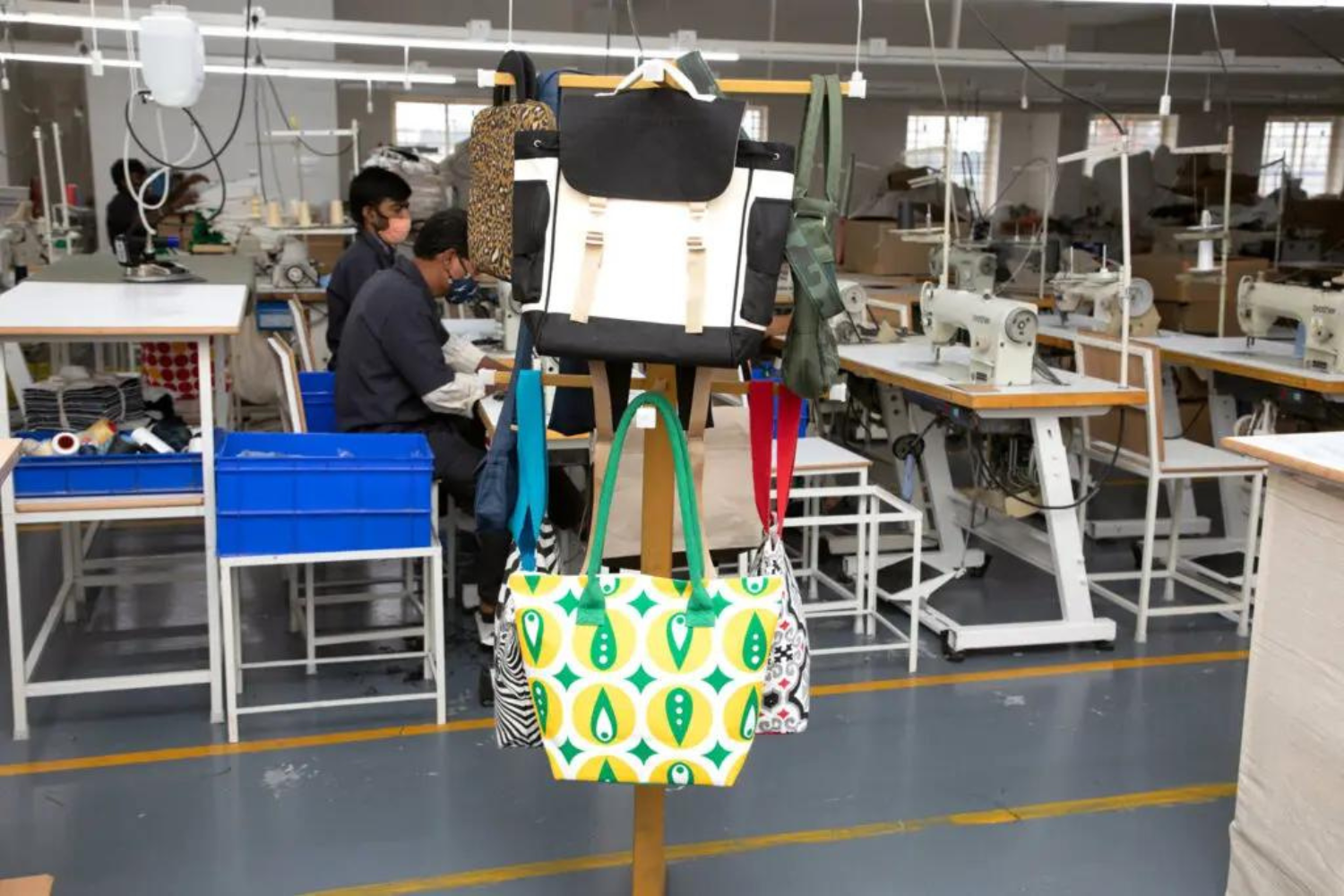
Sampling
We have a separate pattern making and sampling division headed by a Pattern maker and his team of A-class tailors. Simple plain or complex fashion, each and every bag/mask is made after refining the pattern, making some pre-production samples, getting all approvals, and then sent for bulk production. A huge range of samples and product developments keep originating here.
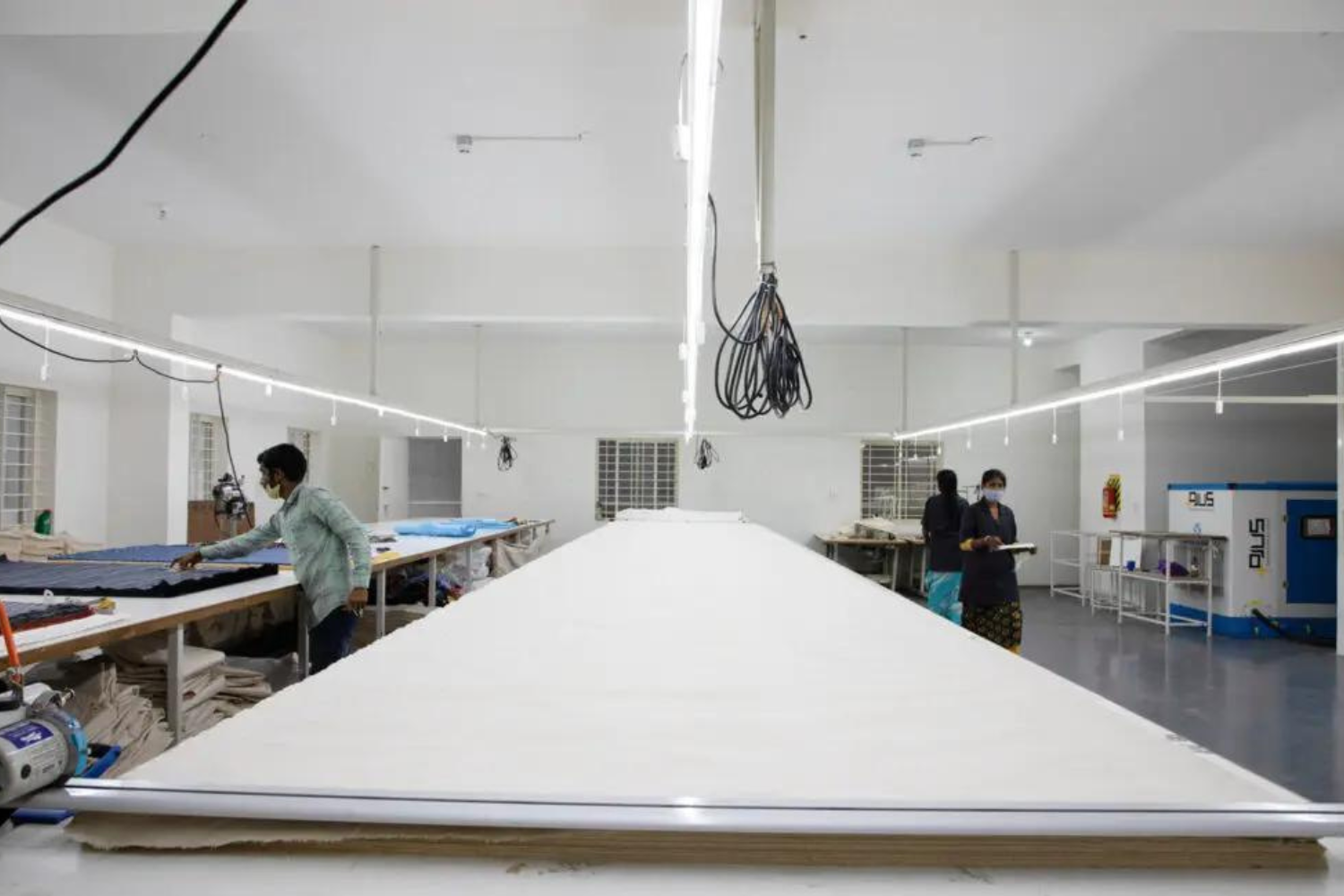
Cutting
The first operation in the manufacturing process after being issued from the store depending upon the style, size, fabric selection is laying the fabric, marking the pattern, and preparing for cutting. We have really long tables, which enables us to have an extensive lay of the fabric. With the use of a straight knife and band knife cutting machines by our experienced cutters, we are able to achieve fantastic efficiency. Low wastage and precision cutting is the hallmark of a good manufacturing setup.
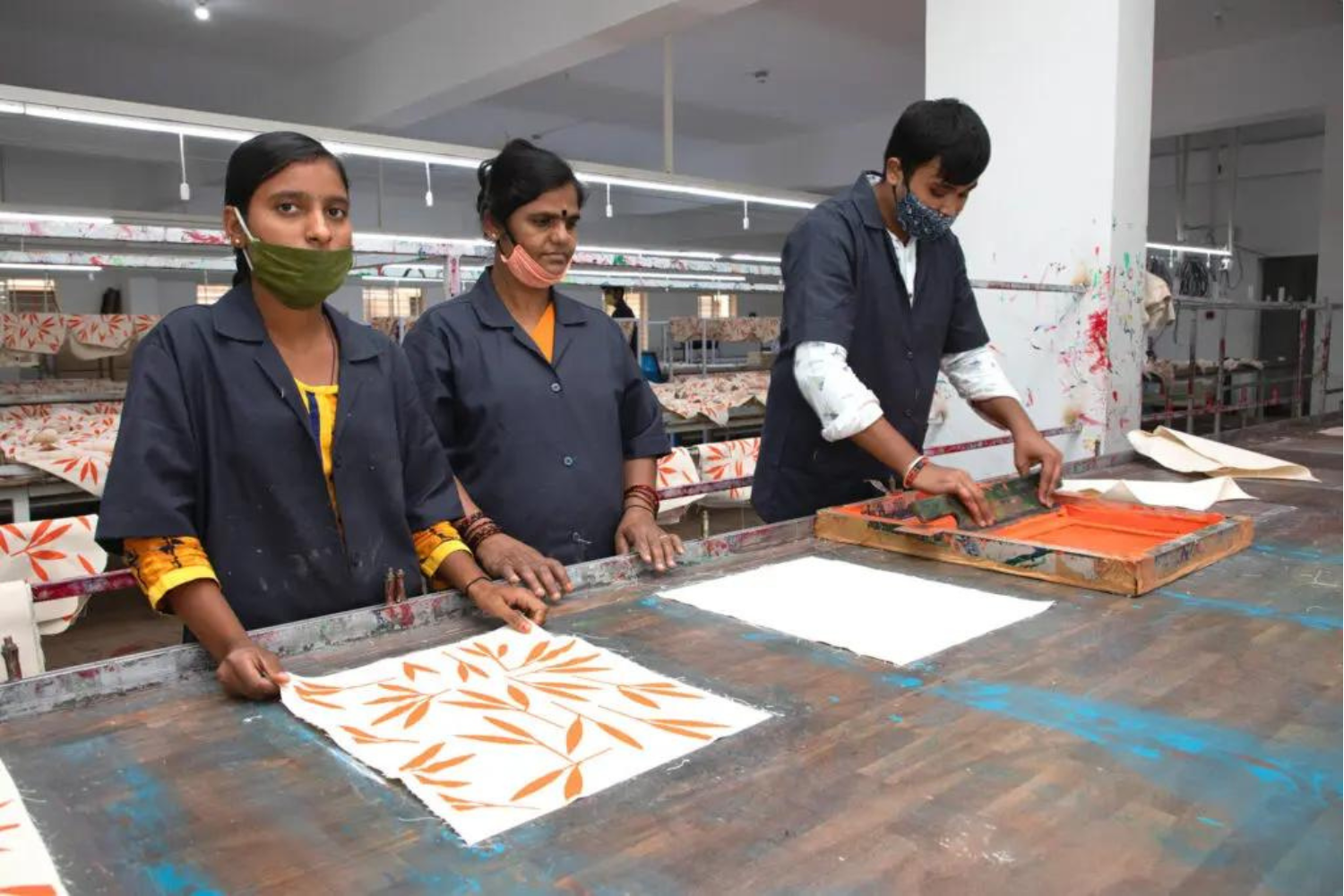
Printing
The cut fabric panels from the cutting section are brought to the Printing section. Printing is done in the traditional way, with the use of screens. We however use only eco-friendly dyes. The dexterity of our printers comes to the fore here, as it is a fine art and requires a very high skill set, which they have acquired through intense training and practice at our training workshops.
The printed fabric panels are then passed through our state of the art Curing machines to reinforce the print and guarantee color fastness.
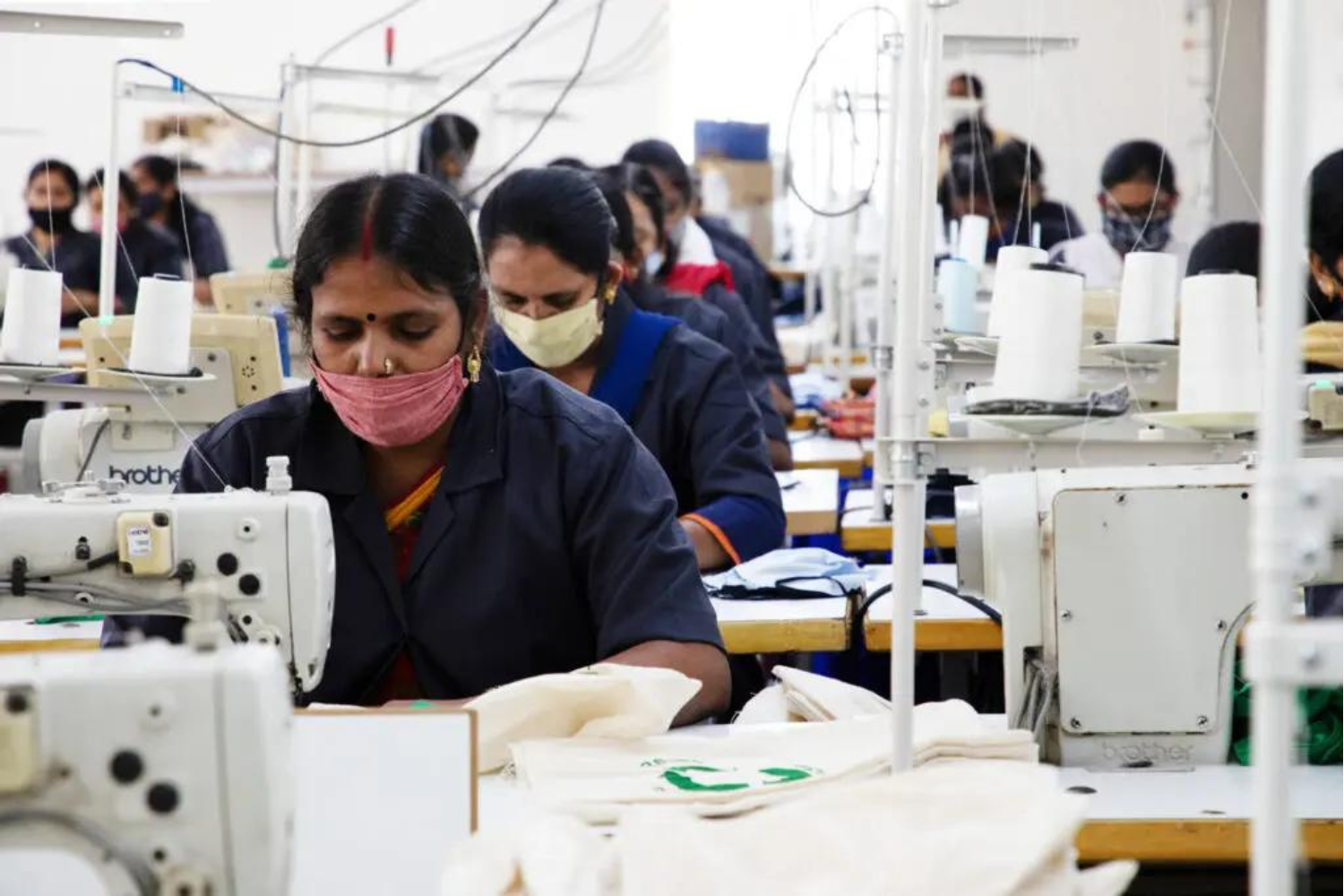
Sewing
The printed panels or plain as the case may be are brought to the sewing section. Each fabric panel is first reinforced using 5 thread over lock machines to ensure there is no fraying at the edges. These are then sewn using Dry bed Juki /Brother single needle machines. The handles are attached, labels/trims affixed and our sent for trimming and ironing.

Trimming
Each piece is trimmed, passed through multiple quality checks, and sent for Ironing. The piece is steam pressed before it is sent to the packing department.
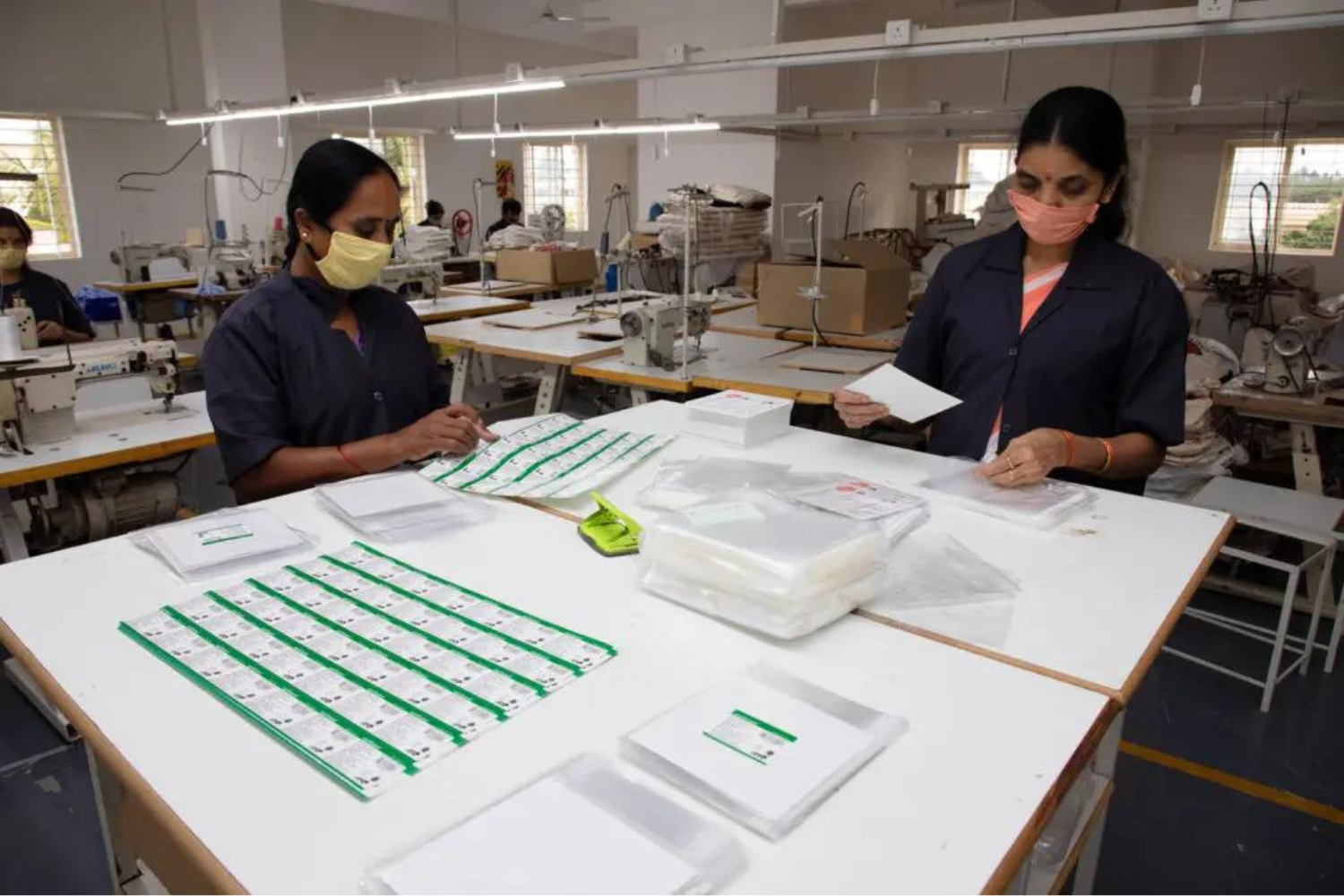
Packing
Each bag is then packed as per the customer’s preference, using eco-friendly products, with minimum use of biodegradable plastic. And is labeled and bar code marked, ready to ship.